Pedaling through city streets has become increasingly challenging with growing traffic congestion. E-bikes offer a promising solution, but their performance hinges on one critical component: the battery. With various options available, choosing the right battery can be overwhelming for manufacturers and riders alike.
E-bikes primarily use lithium-ion batteries1 due to their high energy density, longer lifespan, and lightweight properties. Most modern e-bikes feature 36V or 48V lithium-ion battery systems2 with capacities ranging from 300Wh to 700Wh, providing ranges of 20-80 miles depending on riding conditions, terrain, and assistance levels.
If you're an e-bike manufacturer or enthusiast looking to understand battery technology, you're in the right place. I've spent over a decade working with lithium battery solutions for various applications, and I'll guide you through everything you need to know about e-bike batteries—from their evolution to cutting-edge technologies shaping their future.
The e-bike battery landscape has evolved dramatically since the first commercial models appeared. What began as heavy lead-acid systems has transformed into sophisticated energy storage solutions that balance power, weight, safety, and sustainability. This evolution reflects broader trends in battery technology, with innovations from consumer electronics and electric vehicles finding their way into e-bike designs. Understanding this progression provides valuable context for evaluating current options and anticipating future developments in the field.
What is the History and Background of E-bike Batteries?
The journey of e-bike batteries began with a painful reality: early models were heavy, inefficient, and severely limited in range. Riders faced the frustration of frequent recharging and replacement, while manufacturers struggled to balance performance with practicality. This technological bottleneck prevented e-bikes from achieving mainstream adoption despite their promising potential.
E-bike batteries evolved from heavy lead-acid systems in the 1990s to nickel-based batteries in the early 2000s, and finally to lithium-ion dominance after 20103. This progression has dramatically improved energy density from about 30Wh/kg to over 250Wh/kg today, extending typical ranges from 10 miles to 80+ miles while reducing weight by more than 70%.
The evolution of e-bike batteries mirrors the broader development of portable energy storage technology. When I first entered the industry, I witnessed the transition from bulky lead-acid batteries to more efficient lithium-based solutions. This transformation didn't happen overnight—it represented years of research, engineering challenges, and market adaptation that continue to shape how we power electric bicycles today.
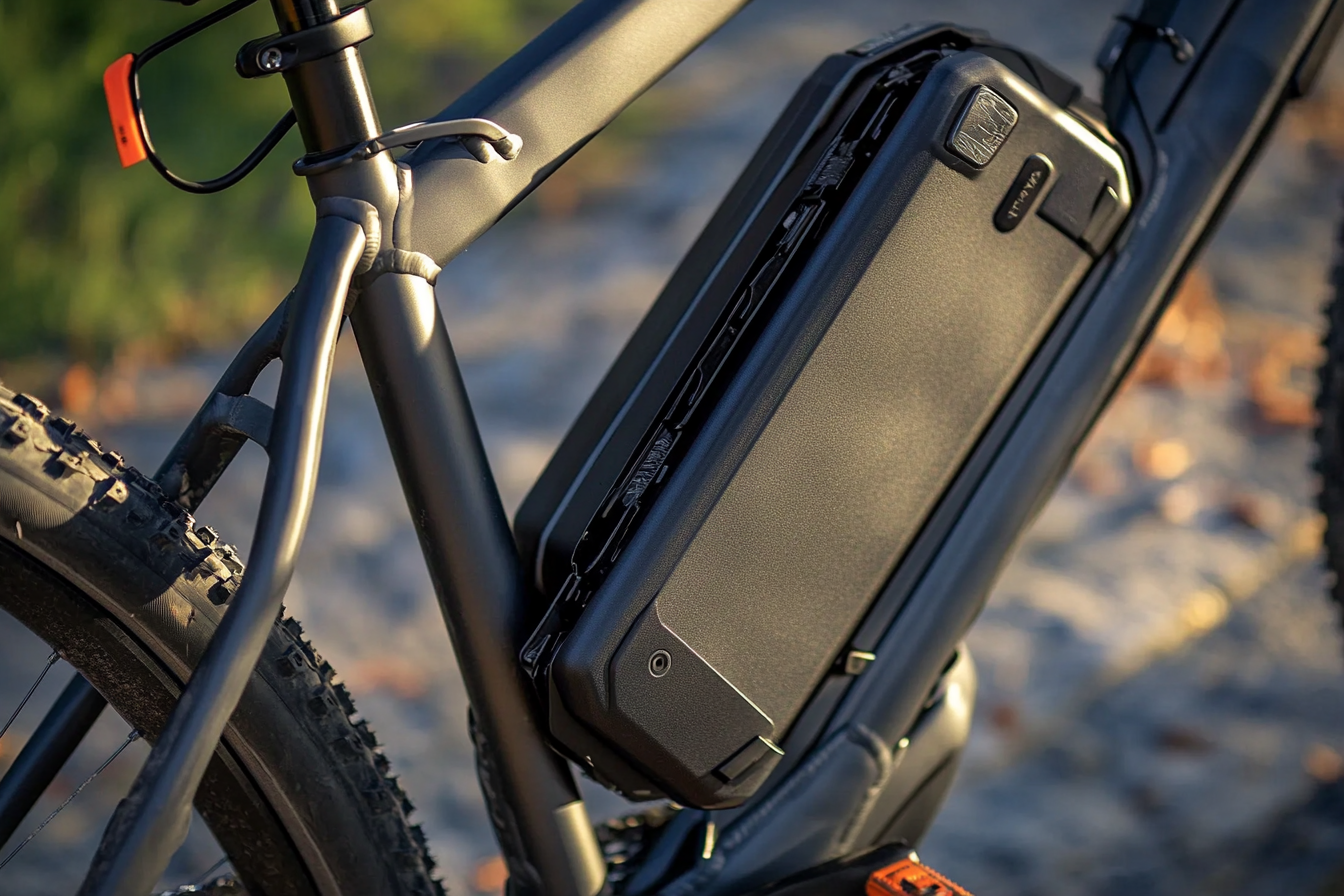
The Lead-Acid Era: Where It All Began
The earliest commercial e-bikes in the 1990s relied almost exclusively on sealed lead-acid (SLA) batteries. These were the same technology used in car batteries, chosen primarily for their low cost and established manufacturing processes. I remember working with manufacturers who were limited by these heavy power sources that could weigh up to 25 pounds for a modest range of just 10-15 miles.
Lead-acid batteries offered simplicity and reliability, but their energy density—typically around 30-40 Wh/kg—created significant design constraints. E-bikes using these batteries were notoriously heavy, often weighing over 70 pounds total. This made them difficult to pedal when the battery was depleted and nearly impossible to carry up stairs or load onto public transportation.
The charging cycle was another limitation. A full recharge could take 6-8 hours, and the batteries typically lasted only 200-300 charge cycles before needing replacement. This translated to a useful life of about 1-2 years for regular commuters, creating both economic and environmental concerns due to the toxic materials in lead-acid batteries requiring specialized disposal.
The Nickel-Based Transition Period
Between 2000 and 2010, we saw a significant shift toward nickel-cadmium (NiCd) and nickel-metal hydride (NiMH) batteries. These offered improved energy density—approximately 60-80 Wh/kg—allowing for lighter e-bikes with increased range. Working with a European manufacturer during this period, I observed how these batteries enabled more streamlined designs that appealed to a broader consumer base.
NiMH batteries, in particular, became popular for mid-range e-bikes, offering about 20-30 miles of range while reducing weight by nearly 40% compared to lead-acid systems. They also demonstrated better performance in variable temperatures, addressing a key complaint from riders in colder climates.
However, these nickel-based solutions weren't without drawbacks. NiCd batteries contained toxic cadmium and suffered from memory effect—a phenomenon where batteries gradually lose capacity if not fully discharged before recharging. NiMH improved on these issues but still faced limitations in charge/discharge efficiency and self-discharge rates that could reach 20% per month when not in use.
The Lithium Revolution
The true game-changer came with the commercial adoption of lithium-ion technology for e-bikes around 2010. Drawing from advancements in consumer electronics and early electric vehicles, lithium-ion batteries offered energy densities exceeding 150 Wh/kg—more than triple that of nickel-based alternatives. This technological leap transformed the e-bike from a niche product to a viable transportation alternative.
I worked closely with manufacturers implementing these new battery systems, witnessing firsthand how they enabled ranges of 40+ miles while keeping battery weight under 7 pounds. The improved power-to-weight ratio allowed designers to create e-bikes that looked and handled much more like traditional bicycles, helping overcome market resistance and stigma.
Beyond performance metrics, lithium-ion batteries brought significant improvements in cycle life (typically 500-1000 complete charges), eliminated memory effect issues, and drastically reduced self-discharge rates to less than 5% per month. These advantages came at a higher initial cost, but the extended lifespan and improved user experience justified the investment for both manufacturers and consumers.
Battery Type | Energy Density | Typical Weight | Typical Range | Cycle Life | Approx. Era of Dominance |
---|---|---|---|---|---|
Lead-Acid | 30-40 Wh/kg | 20-25 lbs | 10-15 miles | 200-300 | 1990-2005 |
NiMH | 60-80 Wh/kg | 12-15 lbs | 20-30 miles | 300-500 | 2000-2010 |
Lithium-ion | 150-265 Wh/kg | 5-8 lbs | 40-80+ miles | 500-1000+ | 2010-Present |
Lithium-ion batteries dominate e-bikesTrue
Lithium-ion batteries are the current standard for e-bikes due to their high energy density and long cycle life.
Lead-acid batteries are still commonFalse
Lead-acid batteries are no longer common in e-bikes due to their heavy weight and low energy density.
What Types of Batteries are Currently Used in E-bikes?
The market presents a dizzying array of battery options, leaving manufacturers confused about which technology best suits their specific e-bike models. This decision becomes even more complex when balancing performance requirements against cost constraints, potentially leading to suboptimal choices that compromise the end-user experience.
Modern e-bikes primarily use lithium-ion batteries in several chemistry variants: Lithium Cobalt Oxide (LCO) for lightweight applications, Lithium Iron Phosphate (LFP) for enhanced safety and longevity, Lithium Nickel Manganese Cobalt Oxide (NMC) for balanced performance, and Lithium Nickel Cobalt Aluminum Oxide (NCA) for high-energy premium models. Each chemistry offers distinct advantages in energy density, cycle life, safety, and cost.
Throughout my career working with e-bike manufacturers across different markets, I've seen how battery selection impacts everything from design possibilities to market positioning. The right battery isn't just a technical specification—it's a strategic decision that shapes the entire product experience. Let me walk you through the main battery types currently dominating the e-bike landscape and help you understand which might be right for your specific application.
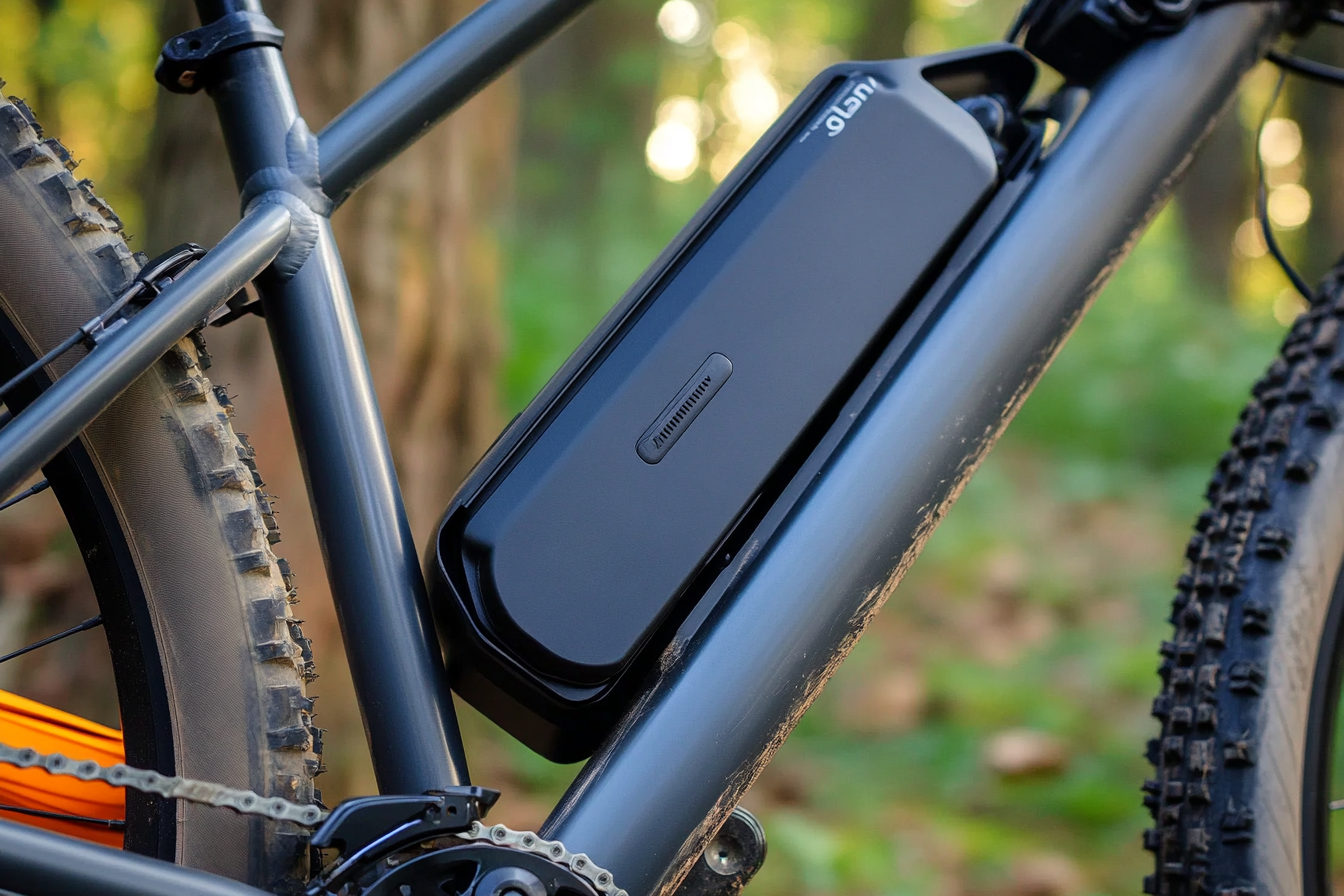
Lithium-ion Variants: The Current Standard
Lithium-ion technology has become the dominant choice for e-bikes, but it's important to understand that "lithium-ion" encompasses several distinct chemistry variants, each with unique properties. The four most common lithium-ion chemistries used in today's e-bikes are Lithium Cobalt Oxide (LCO), Lithium Iron Phosphate (LFP), Lithium Nickel Manganese Cobalt Oxide (NMC), and Lithium Nickel Cobalt Aluminum Oxide (NCA).
When I consult with manufacturers, I often explain that LCO batteries offer excellent energy density (approximately 150-200 Wh/kg) and are commonly used in lightweight, compact e-bikes where space is at a premium. However, they typically offer fewer charge cycles (500-700) and have lower thermal stability compared to other lithium variants. This makes them better suited for casual riders rather than daily commuters or delivery services.
LFP batteries, by contrast, prioritize safety and longevity over maximum energy density. With typical energy densities of 90-120 Wh/kg, they're heavier than other lithium variants but can withstand 1,500-2,000 charge cycles—more than double most alternatives. I've recommended these to fleet operators and rental services where reliability and long service life outweigh the need for maximum range or minimum weight. Their excellent thermal stability also makes them ideal for operations in hotter climates.
NMC: The Balanced Performer
NMC batteries have emerged as the most popular choice for mid-to-high-end e-bikes, offering what I consider the best balance of energy density, power delivery, and cycle life. With energy densities ranging from 150-220 Wh/kg and typical cycle lives of 1,000-2,000 charges, they serve the needs of both daily commuters and recreational riders.
I've worked with several manufacturers who switched from other chemistries to NMC and saw immediate benefits in customer satisfaction. The chemistry allows for sustained power output even as the battery discharges, eliminating the performance drop-off that riders often experience with other battery types when charge levels fall below 30%.
NMC batteries also perform relatively well across temperature ranges, though like all lithium batteries, they experience some capacity reduction in cold weather. The latest generations of NMC cells have improved low-temperature performance, maintaining about 80% of rated capacity at freezing temperatures compared to about 65% for earlier versions.
NCA: The Premium Option
For premium e-bikes where maximum range and performance are paramount, NCA batteries offer the highest energy density currently available in commercial applications—up to 260 Wh/kg. This translates to extended range without adding weight, a critical advantage for performance-oriented e-bikes.
However, this performance comes with tradeoffs in cycle life (typically 500-800 cycles) and higher cost. I generally recommend NCA batteries for high-end models where customers are willing to pay a premium for maximum performance and are likely to replace their e-bikes before battery degradation becomes significant.
The thermal management requirements for NCA batteries are also more demanding, requiring sophisticated battery management systems (BMS) to ensure safety and longevity. This adds complexity to the design process but results in a premium product that delivers exceptional performance.
Battery Chemistry | Energy Density | Cycle Life | Safety Profile | Typical Applications | Relative Cost |
---|---|---|---|---|---|
LCO | 150-200 Wh/kg | 500-700 | Moderate | Lightweight, compact e-bikes | Medium-High |
LFP | 90-120 Wh/kg | 1,500-2,000 | Excellent | Fleet, rental, utility e-bikes | Medium-Low |
NMC | 150-220 Wh/kg | 1,000-2,000 | Good | Mid to high-end consumer e-bikes | Medium |
NCA | 200-260 Wh/kg | 500-800 | Moderate | Premium performance e-bikes | High |
NMC batteries are widely usedTrue
NMC batteries are popular for their balanced performance in energy density, power delivery, and cycle life.
LFP batteries have low energy densityFalse
LFP batteries have moderate energy density but are valued for their safety and longevity.
What are the Main Challenges Associated with E-bike Batteries?
E-bike manufacturers and users alike face significant anxiety about battery safety, with high-profile incidents of thermal runaway and fires damaging consumer confidence. Additionally, the limited range of current batteries creates "range anxiety" among riders, while environmental concerns about battery production and disposal raise questions about e-bikes' green credentials.
The main challenges with e-bike batteries include safety concerns related to thermal runaway risks, limited range causing rider anxiety, high replacement costs (typically $300-$800), weight constraints affecting bike handling, environmental impact from mining and disposal, and compatibility issues between different manufacturers' systems. These challenges significantly affect adoption rates, user experience, and the overall sustainability of e-mobility.
Having worked with dozens of e-bike manufacturers facing these challenges, I've gained valuable insights into both the technical and practical aspects of these limitations. The issues aren't merely theoretical—they directly impact business decisions, product design, and ultimately, the end-user experience. Let's explore these challenges in depth to better understand how they manifest and why they matter.
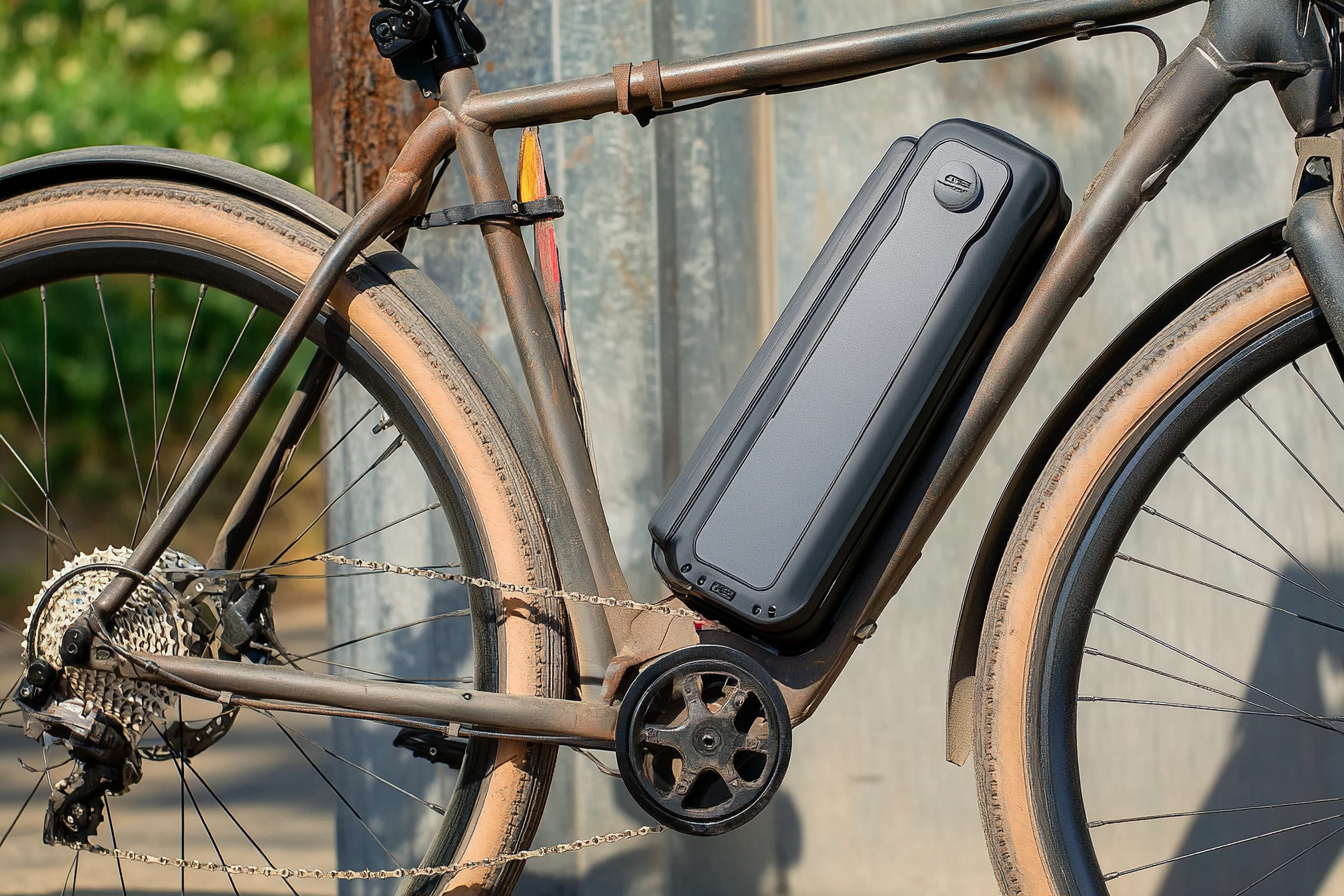
Safety Concerns: The Thermal Runaway Risk
Safety represents perhaps the most critical challenge for e-bike batteries. Lithium-ion batteries store significant energy in a compact space, creating inherent risks if not properly designed, manufactured, and maintained. The primary concern is thermal runaway—a chain reaction where battery cells overheat, potentially leading to fire or explosion.
I've consulted on several cases where manufacturers experienced battery incidents, and the root causes typically fall into three categories: physical damage to cells, manufacturing defects, or charging system failures. Physical damage often occurs from impacts during riding or improper handling during transportation. Even a seemingly minor impact can compromise cell integrity, potentially creating internal short circuits that manifest as failures days or weeks later.
Manufacturing defects present a particularly insidious challenge because they may not be immediately apparent. Microscopic metal particles introduced during production, separator defects, or electrode alignment issues can all lead to eventual failure. This is why I always emphasize the importance of working with reputable battery suppliers who maintain strict quality control protocols and provide comprehensive test documentation.
Charging system failures represent the third major safety risk. Overcharging lithium-ion cells can lead to lithium plating, damaging the cell structure and creating conditions for thermal runaway. Quality battery management systems (BMS) are essential to prevent this, but I've seen many manufacturers attempt to reduce costs by using simplified BMS designs that lack redundant safety features or precise cell-level monitoring.
Range Limitations: The Persistent Anxiety
Despite significant improvements in energy density, range limitations remain a major challenge for e-bike users. The typical range of 20-80 miles (depending on battery capacity, terrain, rider weight, and assistance level) creates what's commonly called "range anxiety"—the fear of being stranded with a depleted battery.
Working with urban delivery companies implementing e-bikes, I've observed how this anxiety affects operational decisions. Riders often recharge batteries before they're fully depleted, effectively reducing the usable capacity and increasing charging frequency. This behavior accelerates battery degradation through increased cycle count and can significantly reduce battery lifespan.
The range challenge becomes even more pronounced in cold weather, where lithium-ion capacity can decrease by 20-40% at freezing temperatures. For year-round commuters in colder climates, this seasonal variation creates inconsistency that undermines confidence in e-bikes as reliable transportation.
Cost Considerations: The Replacement Dilemma
The high cost of battery replacement represents another significant challenge. Quality lithium-ion battery packs typically cost between $300-$800, depending on capacity and chemistry—often representing 30-40% of an e-bike's total value. This creates a difficult decision point when batteries reach end-of-life, typically after 3-5 years of regular use.
I've analyzed the economics of battery replacement for several fleet operators and found that the cost often approaches the depreciated value of older e-bikes. This creates a perverse incentive to replace entire bikes rather than just batteries, generating unnecessary waste and resource consumption.
The situation is complicated by proprietary battery designs that limit replacement options to original manufacturers, often at premium prices. Some manufacturers even use software locks that prevent third-party battery compatibility, creating potential long-term support issues if the original company discontinues the model or exits the market.
Weight and Integration Challenges
Battery weight significantly impacts e-bike handling, stability, and user experience. Even with advanced lithium-ion technology, batteries typically add 5-8 pounds to the bicycle, affecting balance and maneuverability. This weight becomes particularly noticeable when the battery is depleted and riders must rely solely on human power.
The physical integration of batteries presents design challenges as well. Frame-integrated batteries offer aesthetic and aerodynamic advantages but complicate battery removal for charging and limit capacity expansion options. External battery packs provide more flexibility but can compromise the bicycle's appearance and weight distribution.
I've worked with designers struggling to balance these considerations, often finding that optimal technical solutions conflict with marketing preferences for sleek, "bicycle-like" appearances. This tension between form and function continues to challenge the industry as it seeks to broaden e-bike appeal beyond early adopters to mainstream consumers.
Thermal runaway is a safety riskTrue
Thermal runaway in lithium-ion batteries can lead to fires or explosions if not properly managed.
Range anxiety is no longer an issueFalse
Range anxiety remains a significant concern for e-bike users due to limited battery range.
How Can We Address the Challenges of E-bike Batteries?
Manufacturers struggle to balance competing priorities of safety, performance, cost, and environmental impact when developing e-bike battery solutions. Without clear strategies to address these multifaceted challenges, the industry risks stagnation and failing to reach its full potential in transforming urban mobility.
Addressing e-bike battery challenges requires implementing multi-layered safety protocols including improved cell isolation and thermal management, adopting standardized battery systems for interchangeability, developing battery swapping infrastructure, implementing smart BMS systems that adapt to conditions, designing for repairability with modular components, and establishing comprehensive recycling programs that recover over 90% of battery materials.
In my work with e-bike manufacturers and fleet operators, I've helped implement practical solutions to these challenges. The most successful approaches don't rely on a single breakthrough but rather combine incremental improvements across multiple dimensions. Let me share some effective strategies that have proven valuable in real-world applications.
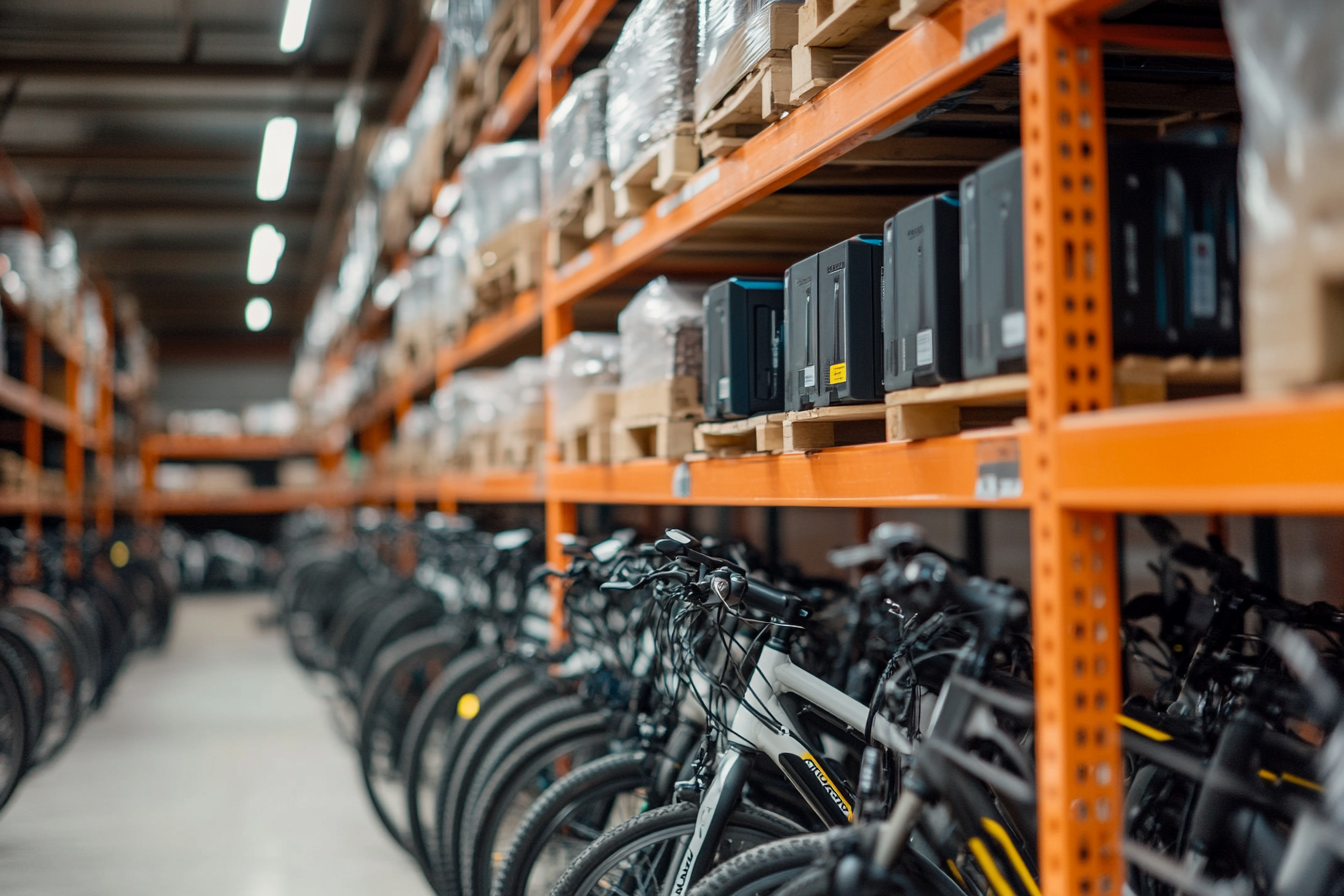
Enhancing Battery Safety Through Design and Materials
Improving battery safety begins at the cell level with enhanced separator materials that prevent internal short circuits even when physically damaged. Working with a manufacturer in Germany, we implemented ceramic-coated separators4 that significantly improved puncture resistance and thermal stability without substantial cost increases.
Beyond cell-level improvements, battery pack design plays a crucial role in preventing catastrophic failures. Effective thermal management systems that isolate individual cells can prevent thermal runaway from propagating throughout the pack. I've helped design systems using phase-change materials5 that absorb excess heat during rapid discharge or charging, maintaining safer operating temperatures across all cells.
Physical protection represents another critical safety element. Impact-resistant casings with crush zones can prevent cell damage during accidents or rough handling. In one project, we developed a honeycomb structure between the outer case and cell array that could absorb significant impact energy without transferring forces to the cells themselves.
Perhaps most importantly, sophisticated battery management systems provide active protection against electrical and thermal abuse. Advanced BMS designs monitor individual cell voltages, temperatures, and internal resistance to detect potential issues before they become dangerous. When working with a major European e-bike brand, we implemented a multi-tiered safety protocol that could detect abnormal cell behavior and automatically adjust charging parameters or disconnect problematic cells.
Standardization and Interoperability Solutions
The fragmentation of battery systems across manufacturers creates significant challenges for users and the broader e-bike ecosystem. I've been advocating for greater standardization of battery interfaces, mounting systems, and charging protocols to address these issues.
Some regional progress has emerged, particularly in Europe where several manufacturers have adopted compatible battery mounting systems allowing interchangeability between brands. This approach benefits consumers through greater replacement options and creates economies of scale for battery producers, potentially reducing costs over time.
Standardized diagnostic interfaces represent another promising area. By adopting common protocols for battery health monitoring and diagnostics, third-party service providers can offer maintenance and repair services across multiple brands. I worked with a service network to implement universal diagnostic tools that could assess batteries from different manufacturers, significantly improving repair options for consumers.
Battery Swapping Infrastructure
Battery swapping offers a compelling solution to range limitations and charging time concerns. Rather than waiting for batteries to recharge, users simply exchange depleted batteries for fully charged ones at swapping stations. I've consulted on several pilot programs implementing this approach for delivery fleets and bike-sharing systems.
The key to successful battery swapping lies in standardized battery modules and automated exchange mechanisms. In Taiwan, I observed a system where delivery riders could swap batteries in less than 30 seconds using a secure automated station. This approach eliminated charging downtime and effectively extended the operational range indefinitely.
For consumer applications, subscription-based battery services show promise. Under this model, users don't own the battery but rather subscribe to a service that provides access to a network of swapping stations. This reduces the upfront cost of e-bikes and shifts battery maintenance responsibility to specialized providers who can optimize battery longevity and performance.
Adaptive Battery Management Systems
Smart BMS technology represents one of the most promising approaches to addressing multiple battery challenges simultaneously. These systems use machine learning algorithms to adapt charging and discharging parameters based on usage patterns, environmental conditions, and battery age.
Working with a technology partner, we developed a system that could extend battery lifespan by up to 40% by analyzing individual riding patterns and optimizing charging accordingly. The system would avoid charging to 100% when full range wasn't needed based on typical usage, significantly reducing calendar aging effects that degrade lithium-ion cells over time.
These adaptive systems can also help manage temperature-related performance issues. By preconditioning batteries before use in cold weather (gently warming cells using internal resistance) and optimizing discharge patterns, they can maintain more consistent performance across varying conditions. One implementation I worked on could maintain 85% of rated capacity at freezing temperatures compared to 65% with conventional BMS systems.
E-bike batteries require multi-layered safety protocols.True
Effective safety measures include cell isolation, thermal management, and smart BMS systems.
Battery swapping is impractical for e-bikes.False
Battery swapping is a viable solution, especially for delivery fleets and bike-sharing systems.
What Technological Advancements are Improving E-bike Batteries?
The rapid pace of battery innovation creates uncertainty for manufacturers about which emerging technologies to invest in, potentially leading to hesitation or misaligned development efforts. Without clear understanding of which advancements offer practical near-term benefits versus long-term potential, companies risk making costly strategic errors in their product roadmaps.
Key technological advancements improving e-bike batteries include silicon-enhanced anodes6 increasing energy density by 20-40%, solid-state electrolytes eliminating flammable components while boosting performance, advanced BMS systems extending lifespan through AI-driven charging optimization, structural battery designs integrating cells into bike frames for weight reduction, and rapid-charging protocols enabling 80% capacity in under 30 minutes without degradation.
Having worked at the intersection of battery technology development and practical implementation, I've gained perspective on which innovations offer immediate value versus those that remain promising but unproven. Let me share insights on the most significant technological advancements reshaping e-bike batteries today and in the near future.
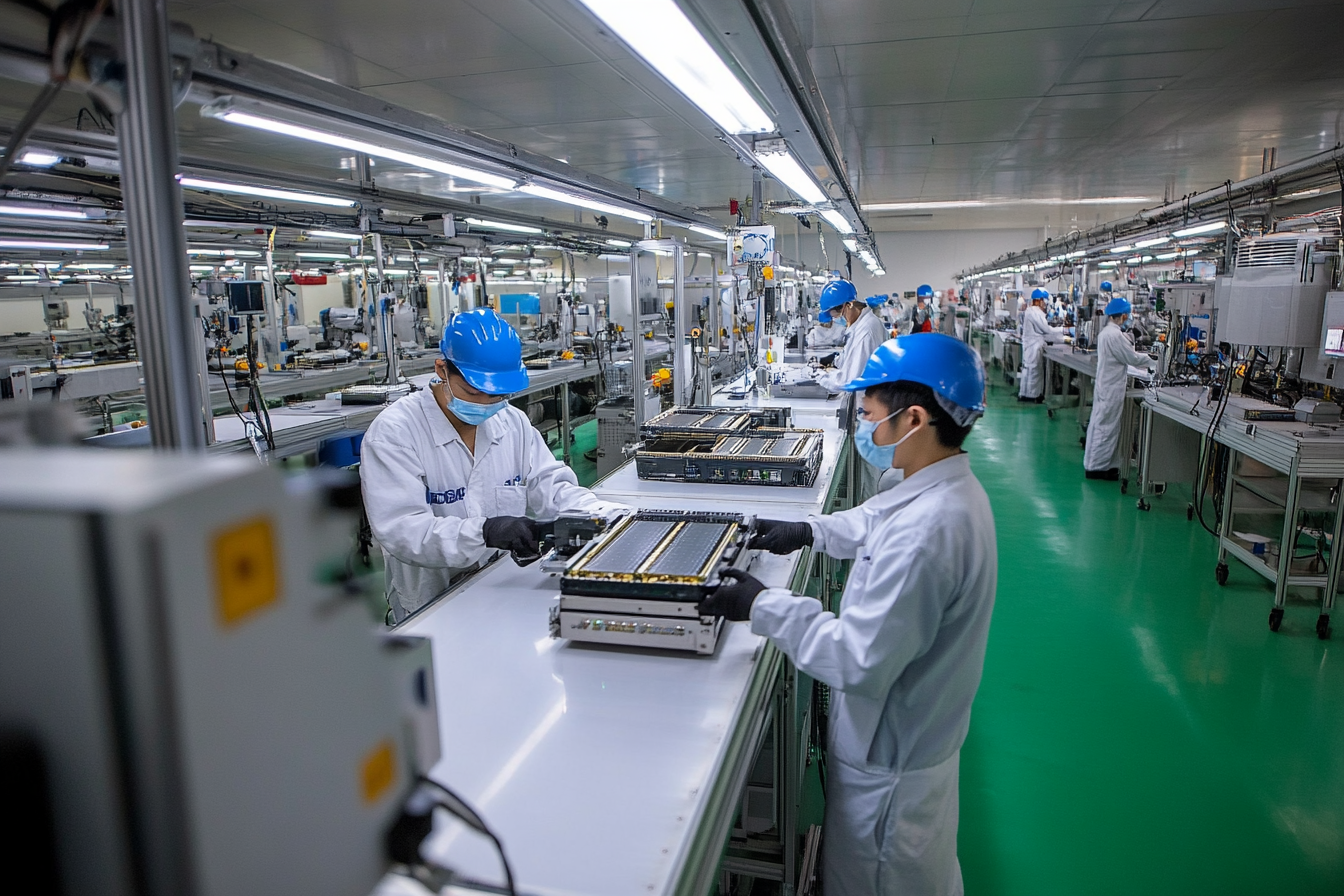
Silicon-Enhanced Anodes: The Near-Term Energy Density Boost
Traditional lithium-ion batteries use graphite anodes, but silicon offers theoretical capacity up to ten times higher. Pure silicon anodes face challenges with expansion during charging (up to 300% volume increase), but silicon-graphite composite anodes provide a practical middle ground, increasing energy density by 20-40% while maintaining acceptable cycle life.
I've worked with manufacturers implementing first-generation silicon-composite anodes in premium e-bike models. These batteries deliver noticeable range improvements without significant cost increases or lifespan reductions. The technology has matured significantly since 2018, with several major cell manufacturers now offering commercial silicon-enhanced cells specifically designed for e-mobility applications.
The implementation requires careful BMS calibration to account for different voltage curves and internal resistance characteristics. In one project, we developed custom state-of-charge algorithms that accurately tracked battery capacity throughout discharge, eliminating the estimation errors common when applying traditional models to silicon-enhanced cells.
For e-bike manufacturers, silicon-composite anodes offer a compelling near-term solution to range limitations without requiring radical redesigns or unproven technologies. The incremental nature of this improvement makes it particularly attractive for immediate implementation while more revolutionary technologies continue development.
Solid-State Electrolytes: The Safety Revolution
Conventional lithium-ion batteries use liquid electrolytes that contribute to fire risk during thermal runaway events. Solid-state batteries replace these flammable liquids with solid electrolytes, dramatically improving safety while potentially enabling higher energy densities and faster charging.
While full commercial implementation remains several years away, I've evaluated prototype solid-state cells from several developers targeting e-mobility applications. These cells demonstrate impressive safety characteristics—maintaining stability even when physically damaged or exposed to extreme temperatures that would cause conventional cells to fail catastrophically.
Beyond safety improvements, solid-state technology offers performance advantages including wider operating temperature ranges and reduced self-discharge rates. Some designs also promise longer cycle life by eliminating side reactions that gradually degrade conventional lithium-ion cells.
The primary challenges delaying widespread adoption include manufacturing scalability and cost. Current production methods for solid electrolytes remain complex and expensive compared to established liquid electrolyte processes. However, significant investment in manufacturing technology suggests these barriers will diminish over the next 3-5 years, potentially making solid-state batteries commercially viable for premium e-bike applications by 2025-2026.
Advanced Battery Management Systems
While much attention focuses on cell chemistry improvements, some of the most impactful near-term advancements are occurring in battery management systems. Modern BMS technology leverages AI algorithms, cloud connectivity, and sophisticated sensing to optimize battery performance and longevity.
I recently collaborated on implementing a machine-learning BMS that analyzes individual cell characteristics and usage patterns to develop customized charging profiles. The system continuously adapts to battery aging, environmental conditions, and usage intensity, extending useful life by up to 40% compared to conventional fixed-parameter systems.
These advanced BMS designs also improve safety through more sophisticated fault detection. By monitoring subtle changes in cell impedance, temperature gradients, and voltage response curves, they can identify potential failure modes before they become dangerous. In one implementation, the system detected and isolated a failing cell that showed no abnormalities under standard testing protocols but exhibited characteristic impedance signatures associated with internal damage.
Cloud connectivity enables additional functionality through over-the-air updates and fleet-wide optimization. For commercial e-bike fleets, these systems can aggregate performance data across hundreds or thousands of batteries, identifying patterns that inform predictive maintenance and operational planning. One delivery company I advised reduced battery-related downtime by 65% after implementing such a system.
Structural Battery Integration
An intriguing development blurring the line between battery and bicycle is structural battery design, where battery cells are integrated directly into the frame structure. This approach reduces weight by eliminating redundant structural elements and potentially increases capacity by utilizing otherwise empty frame volumes.
I've consulted on early implementations of this concept, where battery cells are arranged within carbon fiber composite frames to provide both energy storage and structural integrity. The approach requires close collaboration between battery engineers and frame designers but can yield significant weight savings—up to 20% compared to conventional designs with separate batteries.
Beyond weight reduction, structural integration improves aerodynamics and aesthetics by eliminating external battery packs. This makes e-bikes visually indistinguishable from conventional bicycles, addressing image concerns that deter some potential users.
The challenges of this approach include more complex manufacturing processes, potential serviceability issues, and thermal management considerations. However, for premium e-bikes where performance and aesthetics justify higher production costs, structural battery integration represents an exciting frontier that several manufacturers are actively exploring.
Technology | Current Status | Potential Impact | Timeline for Mainstream Adoption | Key Challenges |
---|---|---|---|---|
Silicon-enhanced anodes | Commercial production | 20-40% energy density increase | Already available in premium models | Higher cost, BMS calibration |
Solid-state electrolytes | Advanced prototyping | Major safety improvement, 50-80% energy density increase | 2025-2026 for premium applications | Manufacturing scalability, interface stability |
Advanced BMS | Early commercial implementation | 30-40% lifespan extension, improved safety | Currently available in high-end systems | Software complexity, sensor integration |
Structural batteries | Prototype/limited production | 15-20% weight reduction, improved aesthetics | 2023-2025 for premium models | Manufacturing complexity, repairability |
Fast-charging protocols | Commercial implementation | 80% charge in 15-30 minutes | Currently available with compatible systems | Thermal management, potential lifespan impact |
Silicon-enhanced anodes increase energy density.True
Silicon-graphite composite anodes can boost energy density by 20-40%.
Solid-state batteries are already mainstream.False
Solid-state batteries are still in development and not yet widely available.
Conclusion
E-bike batteries have evolved dramatically from heavy lead-acid systems to advanced lithium-ion technologies that balance performance, safety, and sustainability. Today's options—primarily NMC, LFP, and emerging silicon-enhanced and solid-state batteries—offer solutions for different priorities. Continuing technological advancements promise to address remaining challenges of range, weight, and environmental impact.
-
Learn why lithium-ion batteries are the top choice for e-bikes ↩
-
Understand the benefits of 36V vs. 48V e-bike batteries ↩
-
Discover the timeline of lithium-ion adoption in e-bikes ↩
-
Learn how ceramic-coated separators enhance battery safety and performance ↩
-
Discover the role of phase-change materials in maintaining safe battery temperatures ↩
-
Understand how silicon-enhanced anodes increase energy density and range ↩