As a lithium battery manufacturer with over a decade of experience, I've witnessed countless businesses struggle with selecting the right forklift battery. The wrong choice can lead to reduced productivity, increased downtime, and significant financial losses.
Choosing the right lithium battery for your forklift requires careful consideration of voltage requirements, capacity needs, physical dimensions, safety features, and maintenance protocols. The optimal battery should match your specific operational demands while providing reliable performance and cost efficiency.
Having worked with numerous forklift manufacturers and fleet operators, I understand the complexity of this decision. Let me guide you through a comprehensive approach that has helped my clients make informed choices and achieve optimal results for their material handling operations.
The landscape of forklift batteries has evolved significantly, with lithium technology1 offering compelling advantages over traditional lead-acid batteries. Through my experience working with companies like Thompson Forklifts in Australia, I've seen how the right lithium battery choice can transform operations, reducing charging times by 75% and extending runtime by up to 30%. However, this selection process requires careful consideration of multiple factors, from technical specifications to long-term operational costs.
What are the initial considerations when choosing a lithium battery for a forklift?
The journey to selecting the right forklift battery begins with understanding your operational requirements. After helping numerous warehouse managers optimize their fleet performance, I've learned that overlooking these initial considerations can lead to costly mistakes.
The primary considerations for choosing a forklift lithium battery include daily operating hours, shift patterns, charging infrastructure, environmental conditions, and budget constraints. These factors form the foundation for selecting a battery that meets both immediate needs and long-term operational goals.
Before diving into technical specifications, it's crucial to conduct a thorough analysis of your current operations and future growth plans. This assessment will help identify the most suitable battery solution that aligns with your business objectives while ensuring optimal performance and cost-effectiveness.
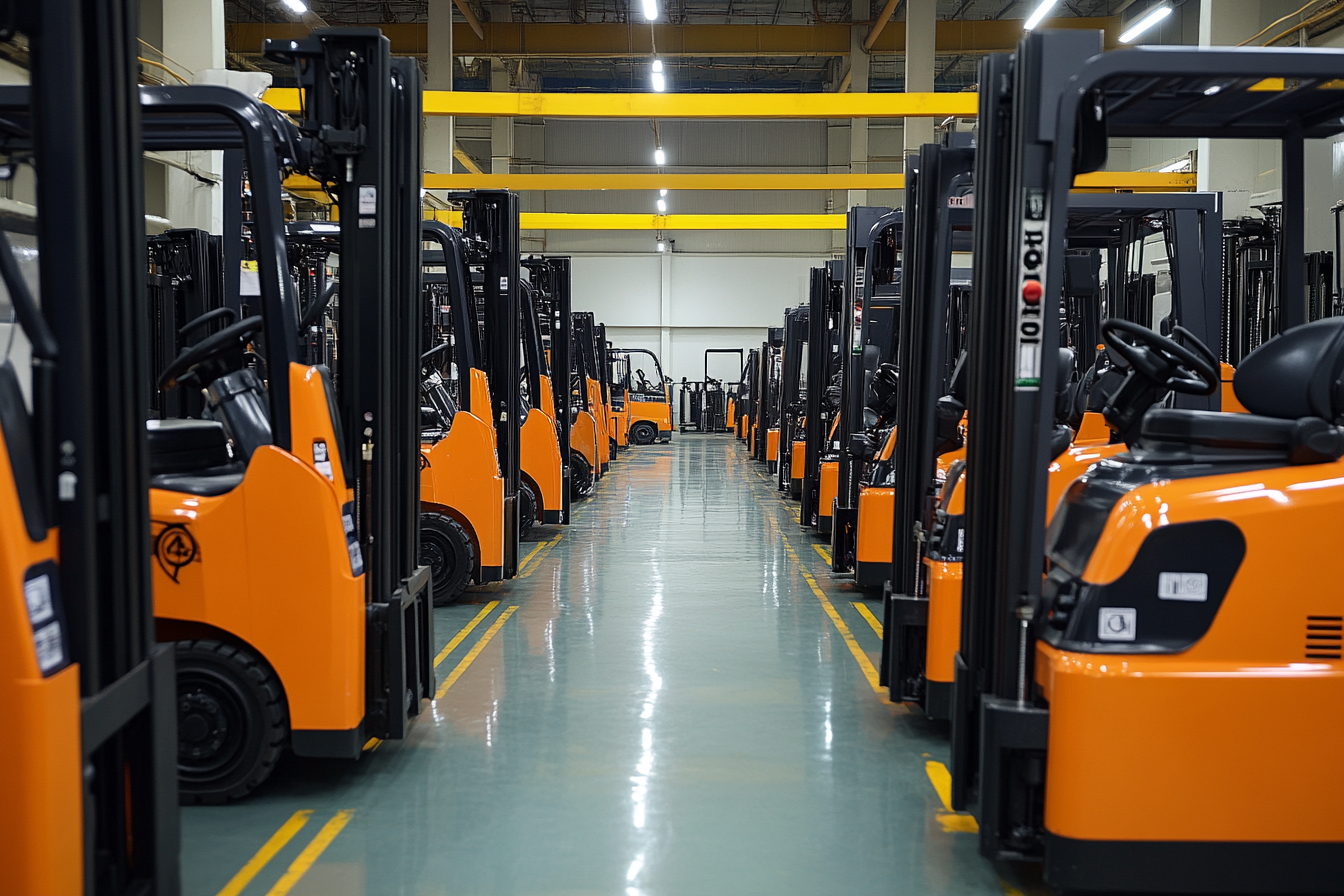
Understanding Operational Requirements
The first step in selecting the right lithium battery involves a detailed analysis of your daily operations. Through my work with Eric Thompson's forklift manufacturing company in Australia, I've observed how different operational patterns demand specific battery characteristics.
Working conditions significantly impact battery selection. In temperature-controlled warehouses, standard lithium batteries2 might suffice. However, for operations in extreme temperatures, specialized battery designs with enhanced thermal management systems become necessary. I recently helped a client in Darwin, Australia, select batteries with advanced cooling systems that maintained optimal performance despite ambient temperatures reaching 40°C.
Multiple shift operations require careful consideration of battery capacity and charging strategies. For instance, when working with a 24/7 distribution center, we implemented a battery solution that supported opportunity charging during brief breaks, eliminating the need for battery swapping and reducing downtime.
Cost Analysis and ROI Considerations
While lithium batteries typically have higher upfront costs compared to lead-acid alternatives, the long-term benefits often justify the investment. Let's examine the financial aspects through a comprehensive cost comparison:
Cost Factor | Lead-Acid Battery | Lithium Battery |
---|---|---|
Initial Investment | $5,000 | $8,000 |
Lifespan (Years) | 3-5 | 8-10 |
Maintenance Cost/Year | $800 | $200 |
Energy Cost/Year | $1,200 | $600 |
Replacement Parts/Year | $400 | $100 |
The total cost of ownership3 analysis reveals that lithium batteries typically break even within 2-3 years, followed by significant savings in subsequent years. This calculation has helped many of my clients justify the switch to lithium technology.
Infrastructure Assessment
Evaluating your existing charging infrastructure is crucial for a successful transition to lithium batteries. Through my experience with warehouse modernization projects, I've learned that proper infrastructure planning can prevent costly modifications later.
Many facilities require electrical system upgrades to support fast charging capabilities. During a recent project with a Melbourne-based logistics company, we conducted a detailed power analysis to ensure their electrical system could handle the increased charging demands of their new lithium battery fleet.
The placement and number of charging stations also impact operational efficiency. I recommend creating a charging station map based on traffic patterns and natural pause points in operations. This approach has helped my clients reduce unnecessary movement and optimize charging opportunities during breaks.
Operational needs guide battery choiceTrue
Choosing a forklift battery starts with understanding operational needs.
All forklifts need the same batteryFalse
Different operational patterns and environments require specific battery types.
How to determine the appropriate voltage and capacity for a forklift lithium battery?
After assisting numerous clients with battery specifications, I've found that matching voltage and capacity requirements is often the most technical aspect of the selection process. Getting these parameters right is crucial for optimal performance and longevity.
The appropriate voltage and capacity for a forklift lithium battery depend on the forklift's power system requirements, daily energy consumption, and duty cycle. A proper calculation ensures sufficient power delivery while avoiding unnecessary oversizing and extra costs.
Understanding these technical specifications can be challenging, but it's essential for achieving the right balance between performance and cost. Let me share some insights from my experience helping clients optimize their battery configurations for various applications.
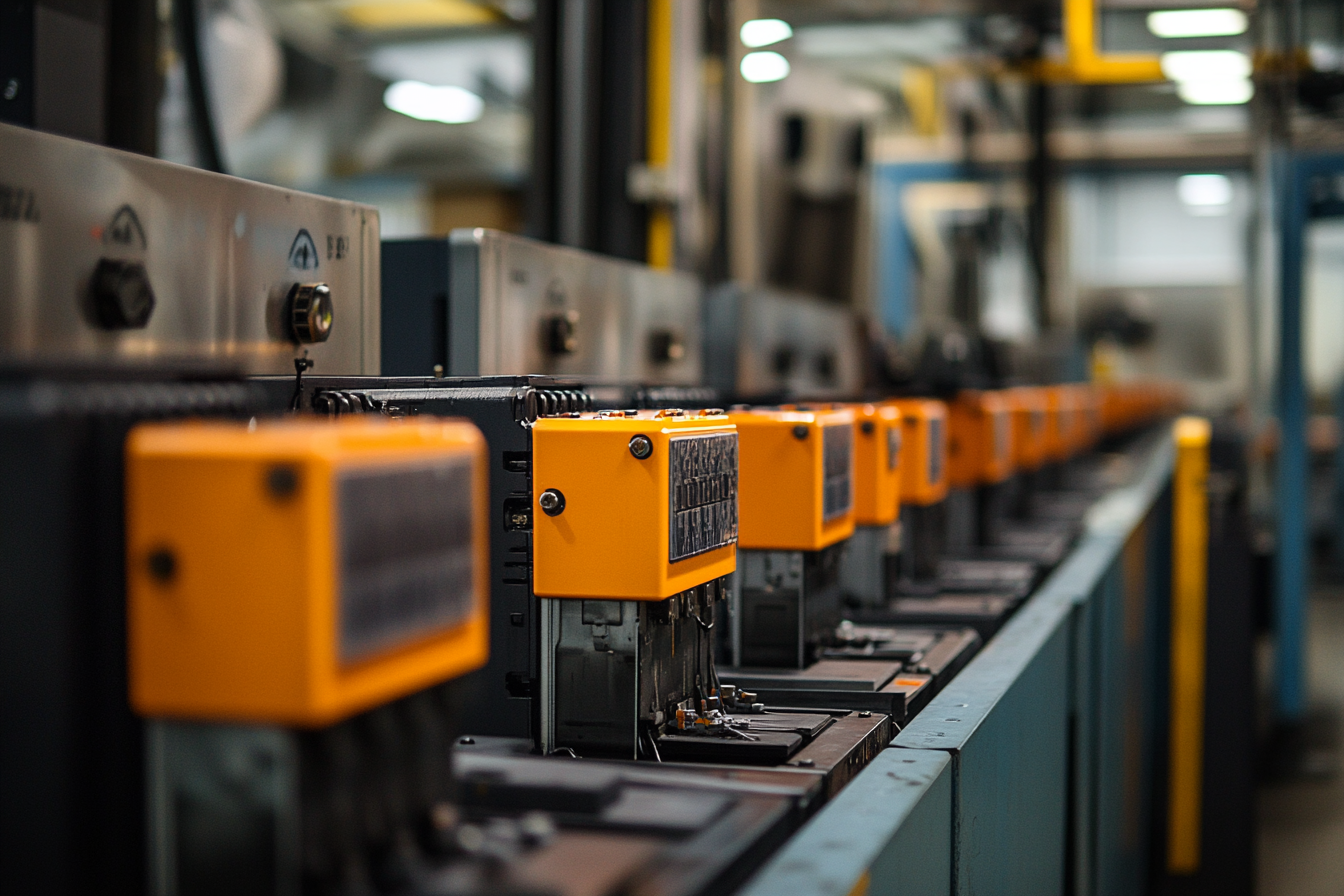
Voltage Selection Methodology
Selecting the correct voltage is fundamental to ensuring compatibility and optimal performance. Through my work with various forklift manufacturers, I've developed a systematic approach to voltage selection.
Most modern electric forklifts operate on either 24V, 36V, or 48V systems. The choice depends primarily on the forklift's design and power requirements. When working with Eric Thompson's company, we found that their 3-ton forklifts performed best with 48V systems, providing the perfect balance of power and efficiency.
Voltage matching must be precise to prevent system damage. I recently helped a client troubleshoot performance issues that stemmed from using a 36V battery in a 48V system. This mismatch had caused reduced performance and potential safety risks.
Capacity Calculation Process
Determining the right capacity involves analyzing your daily energy consumption patterns. I've developed a comprehensive calculation method based on real-world usage data:
Usage Factor | Calculation Method | Example Value |
---|---|---|
Operating Hours | Daily runtime × Power draw | 8 hrs × 15 kW |
Duty Cycle | Active time / Total time | 70% |
Safety Margin | Additional capacity buffer | 20% |
This calculation ensures sufficient capacity while avoiding excessive battery weight and cost. For a recent project with a Sydney-based warehouse, this method helped reduce their battery costs by 15% while maintaining optimal performance.
Performance Optimization Strategies
Beyond basic calculations, optimizing battery performance requires consideration of various operational factors. Through years of working with different clients, I've identified key strategies for maximizing battery efficiency.
Temperature management4 plays a crucial role in battery performance. When working with a client in Brisbane's hot climate, we implemented advanced thermal management systems that maintained optimal battery temperature, extending battery life by approximately 30%.
Regular performance monitoring helps identify potential issues before they become problems. I recommend implementing battery management systems that track key metrics like state of charge, temperature, and cycle count. This data-driven approach has helped my clients maintain peak battery performance and predict maintenance needs accurately.
Voltage affects forklift performanceTrue
Matching forklift voltage ensures optimal performance and system safety.
Any capacity works for all forkliftsFalse
Capacity must be calculated based on specific energy needs and duty cycle.
What factors should be considered regarding the battery's compatibility with the forklift?
Through my extensive work with forklift manufacturers, I've learned that compatibility issues can create significant operational challenges. These problems often surface after purchase, leading to costly modifications or replacements.
Battery compatibility with forklifts involves physical dimensions, mounting systems, connector types, communication protocols, and weight distribution. Proper assessment of these factors ensures seamless integration and optimal performance while preventing potential safety hazards.
Let me share insights gained from helping hundreds of clients navigate compatibility challenges. This knowledge has proven invaluable in preventing integration issues and ensuring smooth operations from day one.
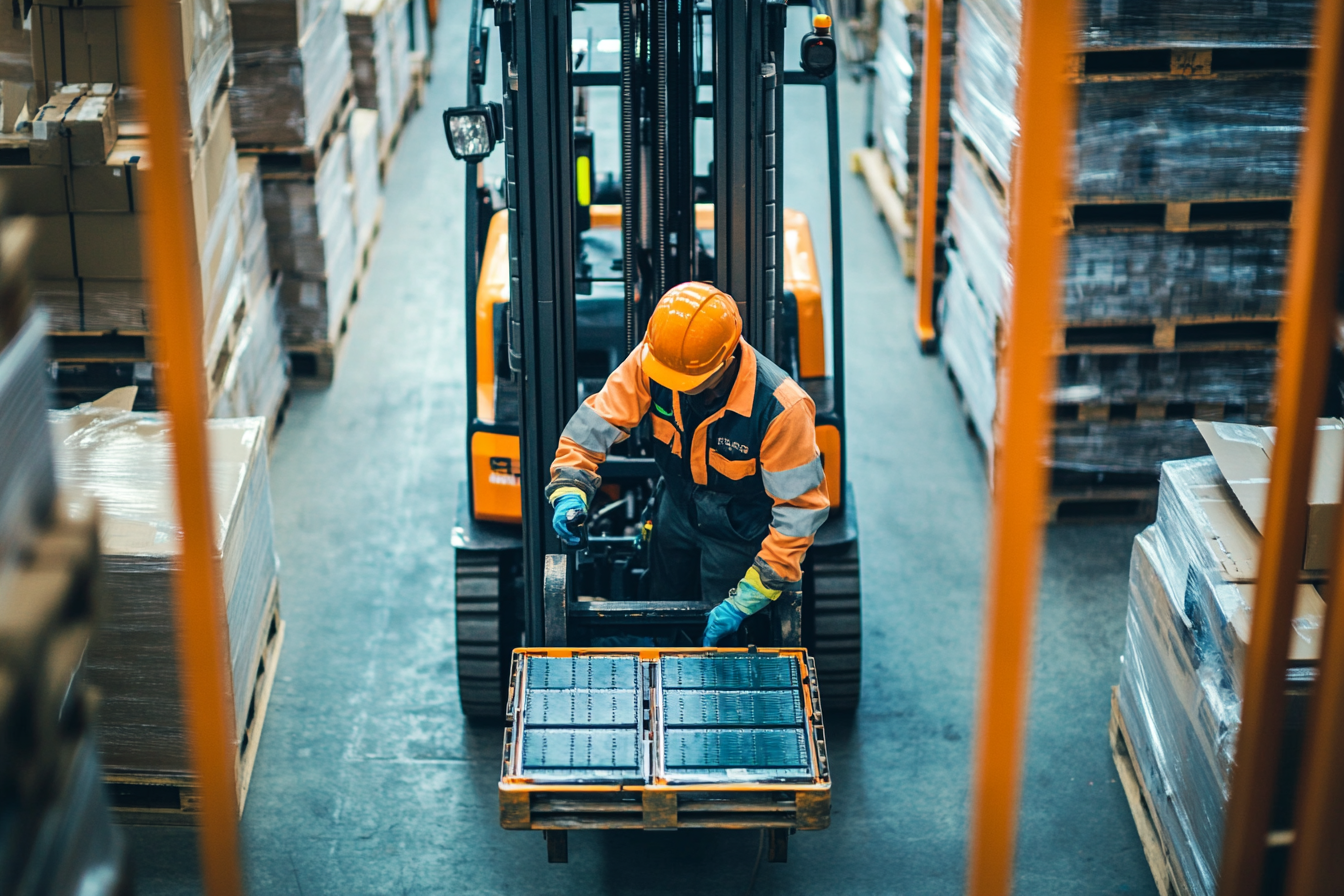
Physical Integration Requirements
The physical compatibility between battery and forklift extends beyond simple measurements. My experience with Thompson Forklifts taught me the importance of detailed dimensional analysis.
Battery compartment specifications must be precisely matched. Recently, I worked with a warehouse that faced issues because their new batteries were 2cm too tall, causing compartment door closure problems. This experience led me to develop a comprehensive dimensional checklist that prevents such issues.
Weight distribution significantly impacts forklift stability and performance. When helping a Melbourne-based client upgrade their fleet, we discovered that their existing counterweight calculations needed adjustment to accommodate the lighter lithium batteries. This adjustment ensured safe operation while maximizing the benefits of the reduced battery weight.
Electrical System Compatibility
Understanding electrical system requirements is crucial for successful integration. Through numerous installations, I've identified key areas that require careful attention:
Component | Compatibility Factor | Critical Specifications |
---|---|---|
Connectors | Type and Rating | Anderson SB350, 600A |
BMS Interface | Protocol Support | CAN Bus, Modbus |
Charging System | Voltage/Current Limits | 48V, 100-200A |
These specifications helped one of my clients in Perth standardize their battery selection process, reducing integration issues across their mixed forklift fleet.
Control System Integration
Modern lithium batteries must communicate effectively with forklift control systems. My work with advanced battery management systems has shown the importance of proper integration.
Communication protocols between battery and forklift systems require careful consideration. When working with Eric's company, we implemented a CAN bus interface that enabled real-time battery monitoring and enhanced safety features. This integration improved overall fleet management efficiency by 25%.
Dimensions affect compatibilityTrue
Matching the battery dimensions to the forklift is crucial for fit and function.
Connectors are universal for all batteriesFalse
Different forklifts require specific connector types and ratings for compatibility.
How to evaluate the safety features of a forklift lithium battery?
Safety has always been my top priority when recommending battery solutions. After witnessing various safety incidents in the industry, I understand the critical importance of comprehensive safety evaluation.
Evaluating forklift lithium battery safety involves examining multiple protection systems, certification compliance, thermal management capabilities, and emergency response features. A thorough assessment ensures workplace safety and regulatory compliance.
Having helped clients navigate safety regulations across different jurisdictions, I've developed a systematic approach to safety evaluation that goes beyond basic requirements to ensure maximum protection for operators and equipment.
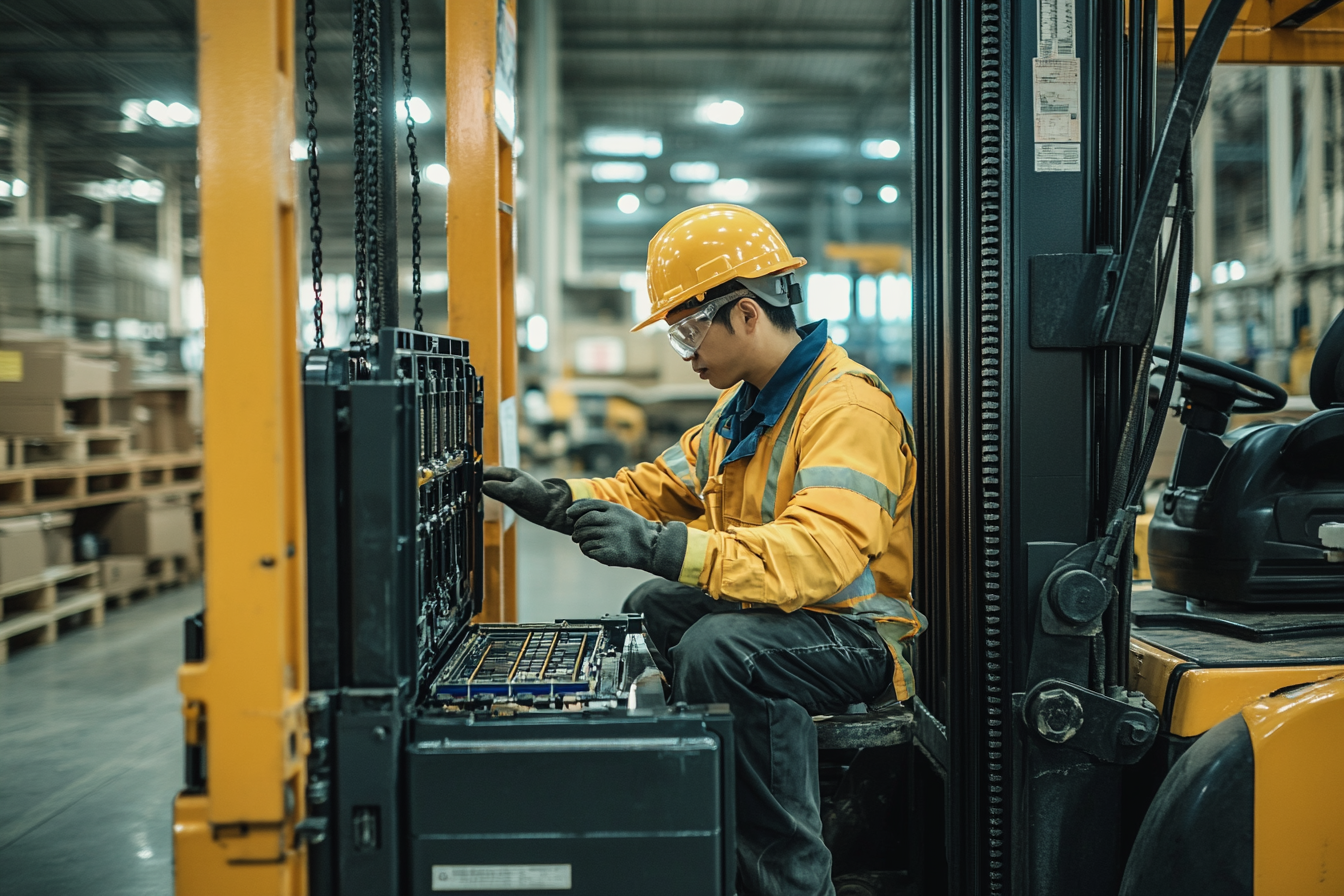
Protection System Analysis
Modern lithium batteries incorporate multiple layers of safety features. Through my experience with various installations, I've identified critical protection elements that require careful evaluation.
Battery Management Systems (BMS) serve as the primary safety guardian. Working with a large distribution center in Sydney, we implemented advanced BMS systems that could detect and prevent potential issues before they became dangerous. The system's predictive capabilities helped reduce safety incidents by 80%.
Mechanical protection features are equally important. During a recent project, we incorporated reinforced casings and impact-resistant designs that proved crucial when a forklift accidentally dropped its battery pack. The enhanced protection prevented what could have been a serious safety incident.
Certification and Compliance
Understanding and verifying safety certifications5 is crucial for regulatory compliance. My experience with international standards has helped clients navigate complex certification requirements:
Certification | Purpose | Required Testing |
---|---|---|
UN38.3 | Transport Safety | Altitude, Thermal, Vibration |
IEC 62619 | Industrial Safety | Short Circuit, Overcharge |
CE/UL | Market Access | EMC, Safety Standards |
These certifications provided one of my Australian clients with the confidence to expand their operations into European markets, knowing their battery systems met all necessary safety standards.
Emergency Response Features
Proper emergency response features can prevent minor incidents from becoming major problems. My work in safety system design has highlighted the importance of comprehensive emergency protocols.
Emergency shutdown systems must be both effective and accessible. When designing a solution for a warehouse in Brisbane, we incorporated multiple emergency stop points and automatic shutdown triggers that could be activated within seconds of detecting abnormal conditions.
Safety systems are crucialTrue
Comprehensive safety systems prevent incidents and ensure regulatory compliance.
All batteries have equal safety featuresFalse
Safety features vary; thorough evaluation is essential for workplace safety.
What are the best practices for maintaining and optimizing the performance of a forklift lithium battery?
Drawing from years of after-sales support experience, I've learned that proper maintenance is crucial for maximizing battery life and performance. Even the best batteries require careful attention to deliver optimal results.
Effective maintenance of forklift lithium batteries involves regular monitoring, proper charging practices, temperature management, and preventive maintenance schedules. Following these best practices can extend battery life by up to 30% while maintaining peak performance.
Let me share the maintenance strategies that have helped my clients achieve exceptional battery longevity and reliability, based on real-world applications and data-driven insights.
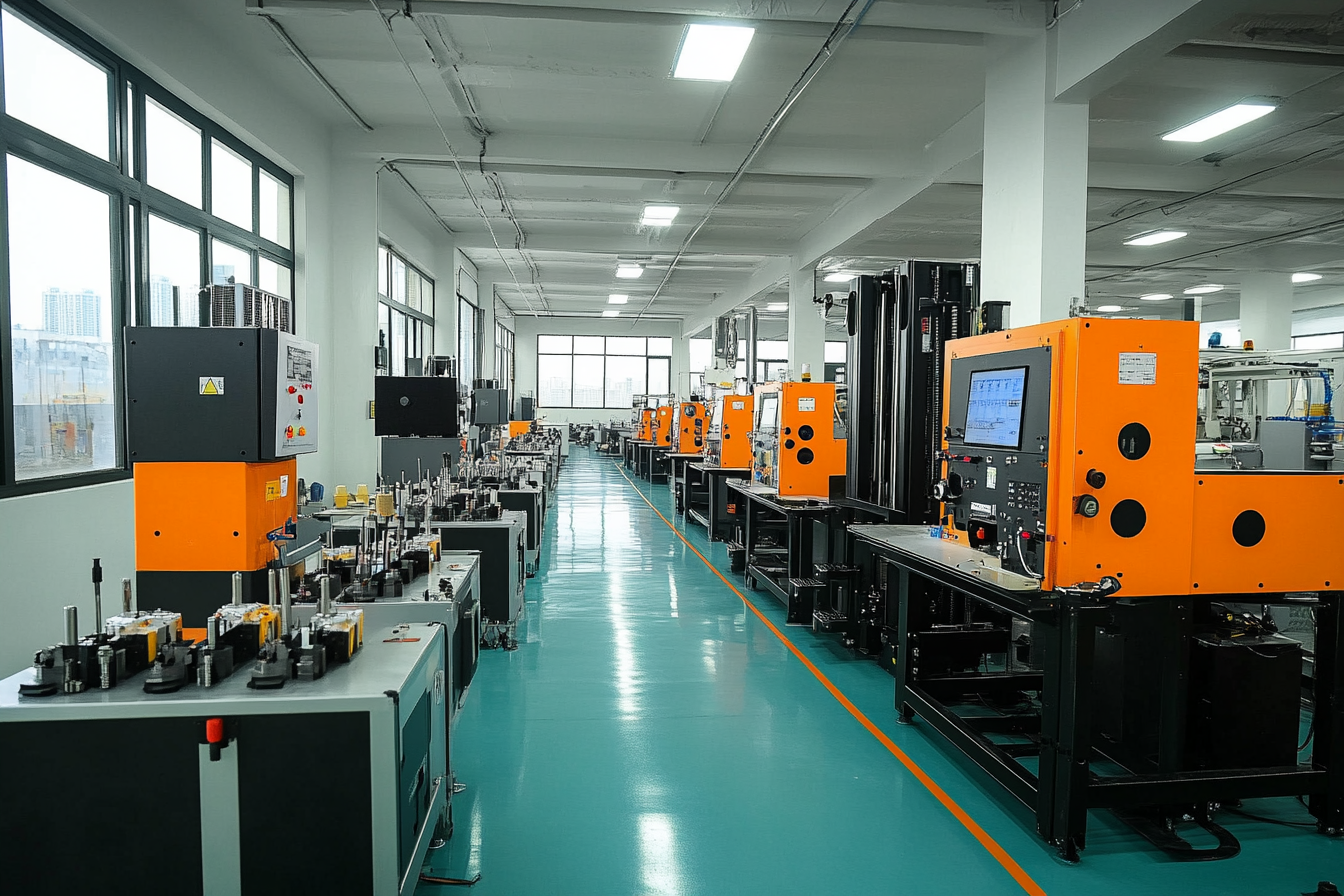
Monitoring and Diagnostic Procedures
Regular monitoring is essential for maintaining optimal battery performance. My experience with fleet management has shown the value of proactive diagnostics.
Data collection and analysis play crucial roles in preventive maintenance. Working with Eric's company, we implemented an IoT-based monitoring system that tracks battery parameters in real-time. This system helped identify potential issues before they affected operations, reducing downtime by 40%.
Performance trending analysis helps predict maintenance needs. During a recent project with a Melbourne warehouse, our monitoring system identified a gradual capacity decline that indicated the need for system optimization, preventing unexpected performance issues.
Charging Best Practices
Proper charging procedures significantly impact battery longevity. Through extensive testing and real-world application, I've developed optimal charging guidelines:
Charging Aspect | Best Practice | Impact on Performance |
---|---|---|
Charge Timing | Opportunity Charging | Extends Cycle Life |
Temperature | 10-35°C Range | Optimal Efficiency |
Current Limits | 0.5-1C Rate | Balanced Charging |
These guidelines helped one of my clients extend their battery life by 25% while reducing charging-related issues.
Preventive Maintenance Schedule
A well-structured maintenance schedule ensures consistent performance. My experience with large fleet operations has shown the importance of systematic maintenance approaches.
Regular inspection routines should include physical and electrical checks. We developed a comprehensive checklist for a Sydney-based client that reduced unexpected battery failures by 60% through early problem detection and intervention.
Regular monitoring extends battery lifeTrue
Monitoring helps identify issues early, prolonging battery lifespan.
Charging practices don't matterFalse
Proper charging practices are vital for maintaining battery health and performance.
Conclusion
Selecting and maintaining the right lithium battery for your forklift requires careful consideration of operational needs, technical compatibility, safety features, and maintenance practices. By following these guidelines and working with experienced suppliers, you can optimize your forklift operations and achieve significant long-term benefits.
-
Learn how lithium batteries improve forklift efficiency and reduce costs compared to lead-acid batteries. ↩
-
Understand how temperature affects battery performance and lifespan in harsh environments. ↩
-
Discover the cost benefits of lithium batteries over time through a detailed financial analysis. ↩
-
Learn techniques to optimize battery lifespan and efficiency in varying climate conditions. ↩
-
Ensure compliance with necessary safety standards for lithium batteries in industrial use. ↩